
The top for the table is built from two layers of 3/4 inch thick Birch plywood. Obviously that would be a very serious situation and one to avoid at all costs. I do this to avoid any chance of wood on the table saw hitting the leading edge of the outfeed table and causing a binding situation. I keep my outfeed table approximately 1/16 of an inch lower than the table saw cast iron top. These allow me to level the top with respect to the table saw. The supports not only help keep the frame square but they also gave me a location to screw the top to the frame from below.Įach of the legs has a heavy-duty adjustable leg attached to it. Lastly you can see I installed corner supports again using pocket screws. I positioned the middle shelf at a height so that my DEWALT TSTAK organizers would fit just below it. The middle shelf consists of one layer of 3/4″ plywood screwed down to the lower rail supports. These are screwed to the inside of all the legs. After building all the legs I cut 3-1/2″ wide support rails for the top and middle shelf. In the photo above you can see how the legs are pocket screwed together (Kreg Jig). For the center two legs I used single pieces of plywood so they would not interrupt the middle shelf.
#UNISAW TABLE SAW INSTALL#
I calculated the height of the table to match the table saw and then subtracted 1 inch (so I could install adjustable leg supports for fine tuning the table height).

I used my Kreg Jig to screw them together in an L-shape. First I built legs using 3-1/2″ wide pieces of plywood. I have lots of it hanging around the shop from a recent cabinet project so it was a great way to use it up. For this table I wanted to have plenty of easy access storage for tools, jigs and materials.Ī majority of the frame was built with scrap 3/4″ cabinet grade Birch plywood. Outfeed tables can take up lots of valuable floor space. Storage – Last but certainly not least is storage.If the table is higher at all it could cause a nasty kickback. Vertical Adjustability – Outfeed tables need to be adjusted such that they are precisely level (or just lower and level) than the table saw surface.Hold Downs – clamping items to a work bench or assembly table is essential because most clamps cannot reach around the large table surface.Bench Vise – Because this table is also my assembly table and general purpose workbench it needed a vise.Sturdy and Strong Design – The table had to be strong enough to support large projects, heavy sheets of wood and hold those materials without much movement.Durable Surface – The table needed a durable surface that’s also smooth so materials can easily slide along the table when then come off the Unisaw.Essentially the table has to be wide enough so the outside edge is more than 48 inches from the back of the saw blade.
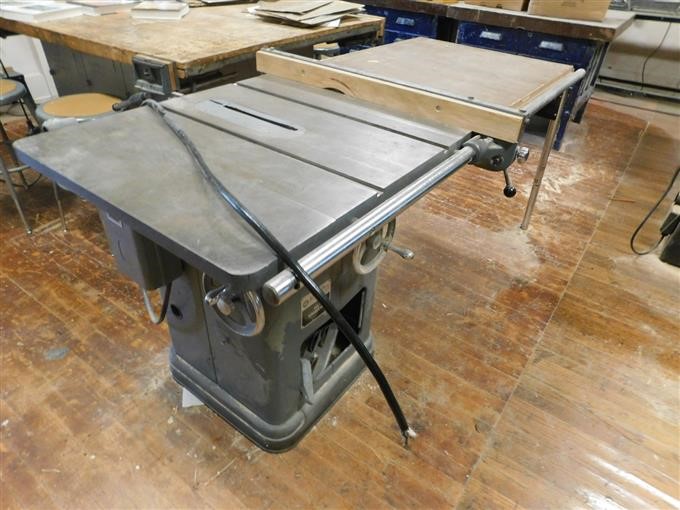
Large Flat Surface – The table needed to be large enough such that I can rip cut an 8′ sheet without the sheet “tipping” over and falling off the table.(Note: in a perfect shop setup it’s ideal to have a separate dedicated assembly table, this way you can still cut materials at the table saw without moving everything from the “assembly table”.) For my outfeed/assembly table I wanted it to include the following features: Due to that limitation I also wanted this outfeed table to serve as an assembly table. My shop is limited on floor space so every inch really does count. In this article I’d like to share a design that I created for an outfeed table that matches my Delta Unisaw. In addition, they often serve as an assembly table and storage cabinet. They making cutting large sheet stock easier, safer, and more accurate. Outfeed tables are one of the most useful companions of a table saw. Custom Outfeed Table Built To Match Unisaw
